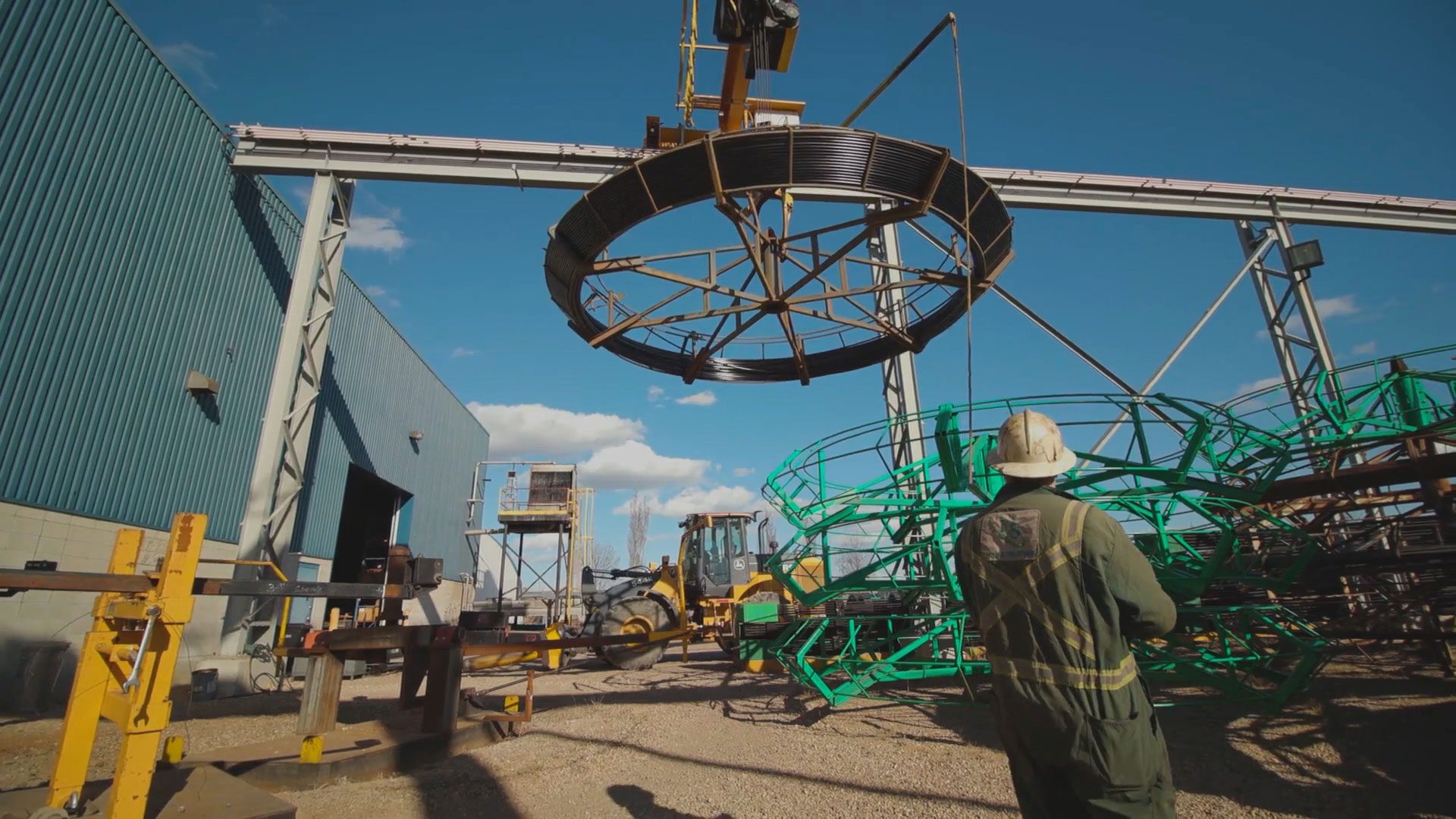
Coated Endless Rod CER Ethyflex
Project Information
Location: | Provost, Alberta, Canada |
LS Product: | 1″ Grade D Coated Endless Rod EthyFlex |
Install Date: | November, 2020 |
Client Challenge
Accelerated rod string failures due to corrosive elements in the produced fluid resulted in a high workover frequency increasing lifting costs due to poor overall performance. Typically, rod string design for corrosive fluids involves improved metallurgy through engineering and selection of corrosive resistant alloys. Rod strings in non-corrosive applications are made from carbon steel. The addition of chromium, molybdenum, and nickel significantly improve the corrosion resistance of these alloy steel grades.
The presence of hydrogen sulfide (H2S), chlorides (salts) and carbon dioxide (CO2) are all contributing factors to the corrosion of downhole equipment containing steel. The pH/acidity of the raw fluid also needs to be considered due to the chemical reaction with hydrogen resulting in corrosion and embrittlement of the metal used in the wellbore. Corrosion from sulfate reducing bacteria introduced to the reservoir through various forms of fluid injection may also contribute to corrosion and surface embrittlement.
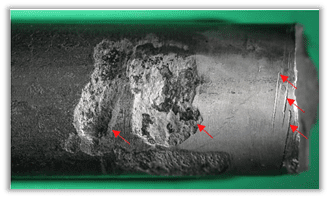
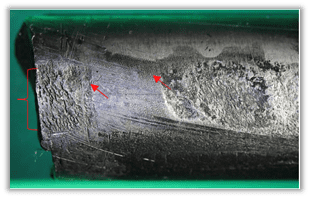
Client Goal
Historical rod string configuration resulted in frequent failures requiring costly workovers. The client company was looking for improvements to increase overall runtime. Corrosion (chemical) inhibition programs were costly resulting in the continuous use of costly downhole chemicals resulting in reduced economic feasibility of producing the well. Significant improvement to the pump configuration and rod string were needed to extend the mean time to failure. Several parted rod samples were sent to the Lifting Solutions materials lab in Edmonton for detailed inspection. Results of the inspection were helpful in understanding the various factors and their contributions to the failure mode.
Our Solution
As a reservoir produces over its lifespan, the existing gas cap will become depleted resulting in a reduction in reservoir pressure. The perforations may also be exposed to bottom water resulting in a produced emulsion that includes oil, water, and gas. The production of the primary gas cap results in free gas in the wellbore emulsion that can contain sour gases and corrosive water elements. For this reason, Grade D CER EthyFlex was installed to mitigate the effects of corrosion by creating a barrier between the steel rod and the produced fluid emulsion.
When corrosion of the rod string occurs, it experiences “pitting” which creates a concentrated fatigue point or stress riser that will fracture and propagate across the rod body due to cyclic, torsional, and axial load fluctuations during operation. In deviated/horizontal wellbores, the cyclic load nature of the configuration results in millions of fatigue cycles experienced by the rod string. The original rod string experienced pitting and magnified stress at the base of this pitting. Coated rod contains a poly-coating layer on the outside of the rod that prevents corrosive/abrasive fluids from attacking the metal and, therefore, eliminating the corrosion pit and stress concentration point resulting in increased longevity of the rod string.
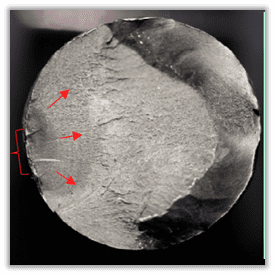
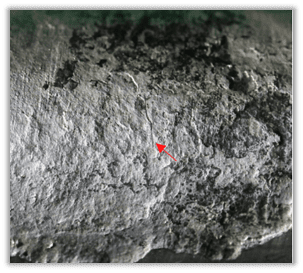
Original attempts to increase the rod string longevity included oversizing the pump in relation to the well performance to operate at an extremely low speed resulting in less overall bending cycles on the rod string. Counterintuitively, the larger the pump configuration required much higher operational torque resulting in a net negative effect on the overall rod string performance. The early crack propagations and stress risers created by the corrosive environment were adversely affected by the higher torque. Decreasing the nominal pump size to better fit the application reduces the torque and helps to mitigate any early rod string failures initiated by corrosion.
Conclusion
After the inspection determined there is significant amounts of H2S and CO2, the use of CER EthyFlex will eliminate corrosion while the coating is intact. The coated rod string has effectively prevented corrosion pitting, therefore reducing failures, and costly workovers. As of the writing of this document, CER EthyFlex string has been in operation for just under 600 days. After exceeding the target four (4) months run, the client has installed several additional CER strings in similar applications that continue to outperform the historical bare continuous rod installations.
Let’s solve your lift challenges.
Reach out and Experience Performance with Lifting Solutions.