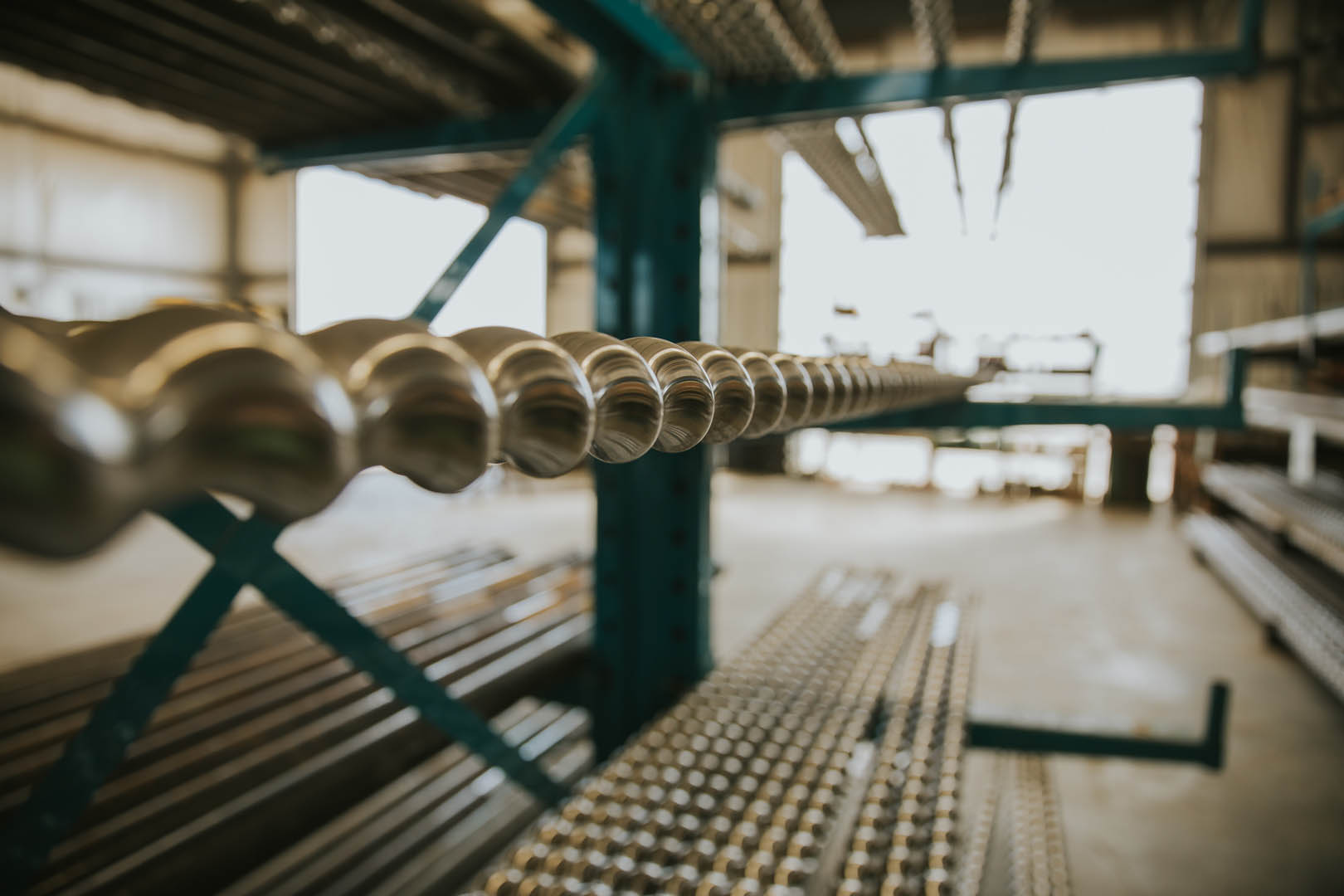
Reduction in Fluid Washing Failures in Heavy Oil | CS-005
Project Profiles
Project Information
Client Name: | Confidential |
Location: | Lloydminster, Saskatchewan, Canada |
Field Application: | Cold Heavy Oil Production with Sand (CHOPS) |
Initial Install Date: | January 2021 |
Product(s): | Soft Nitrile (SN) Elastomer |
CAse Summary
Nitrile elastomers have good resistance to oil, water and abrasives. They have high elasticity and flexibility which makes them an ideal choice for Progressing Cavity Pumps (PCP). The elastomer is one of the most critical components of the stator and are available in two types recommended for Heavy Oil applications. Medium Nitrile (MN, 65-70 Shore A Hardness) and Soft Medium Nitrile (SN, 55-60 Shore A Hardness). The primary difference between these two elastomers is hardness. When the elastomer hardness is decreased in the case of SN we see improvement in the mechanical properties including tear strength and elongation. This improves the ability to handle abrasives/solids while reducing damage to the elastomer at the sealing surface.
Pumps with SN elastomer require higher compression fit sizing between the rotor and stator to achieve similar results as MN elastomer. This higher compression set results in more interference fit and allows for significantly more material loss before complete seal degradation and volumetric efficiency decline. This has also been proven to extend run time before failure due to fluid washing because of slippage in the low efficiency state. This is primarily due to the increase in interference fit, and the improved mechanical properties of the SN elastomer.
Background – Fluid Washing in Abrasive applications
Long term monitoring of applications where both MN and SN elastomers have been deployed has shown an improvement in run time of the SN elastomer when exposed to similar conditions. This includes minimum variability in application and operational parameters (similar well conditions, production conditions and operating methodologies).
Client Challenge
Over a 5-year timeframe, we monitored (and continue to monitor) dozens of MN applications where fluid washing was a frequent repeating failure mode and SN elastomer was recommended as the solution. These CHOPS PCP applications were exclusively in the Heavy Oil region around Lloydminster, AB/SK. The elastomer was exposed to difficult pumping conditions including the production of 10 degree API heavy oil with frequent slugging of sand and water in both vertical and horizontal wellbores. The advantages of a vertical wellbore included the ability to exclude gas from the produced emulsion by setting the PCP intake below perforations to take advantage of natural gas separation up the casing annulus. In horizontal wells this is more difficult because the emulsion comes from below the pump intake resulting in the addition of free gas to the equation, further increasing slippage rates.
Several comparative well histories are documented in the tables below grouped by field and well ID.
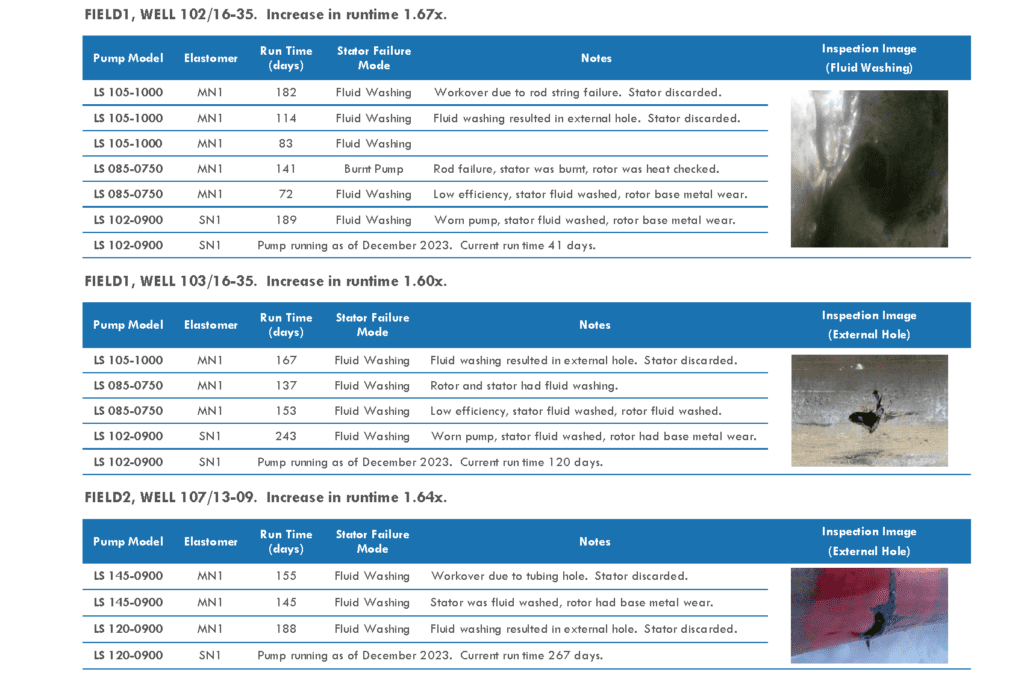
Conclusion
In applications with high amounts of abrasives, Soft Medium Nitrile (SN) has proven to increase run times when exposed to similar conditions as its Medium Nitrile equivalent. These improvements in run time are related to improved mechanical properties (specifically tear strength and elongation). The softer elastomer also requires higher compression between the rotor and stator while maintaining resiliency in the presence of abrasives.
In cases where fluid washing is a common failure mode due to the presence of abrasives and an eventual breakdown of the rotor/stator sealing surface, SN elastomer has repeatedly shown improvement in run times averaging 1.6 times their MN counterparts.
Let’s solve your lift challenges.
Reach out and Experience Performance with Lifting Solutions.