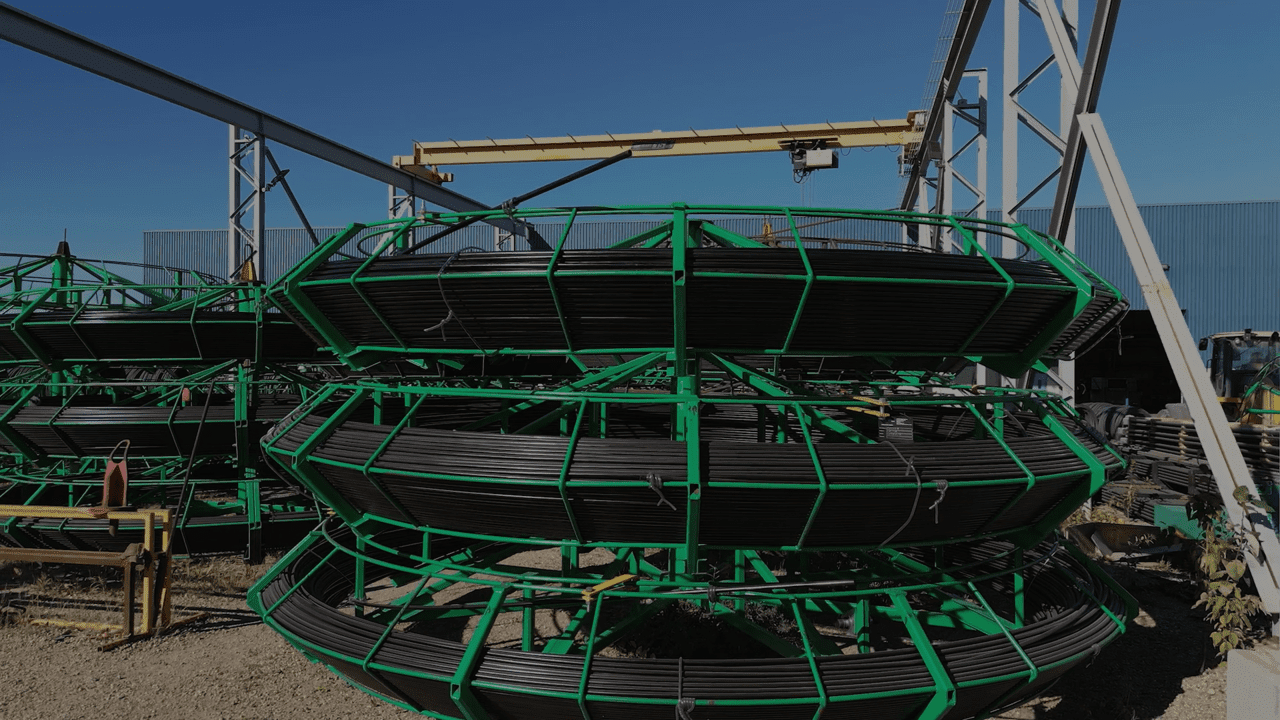
KeBond Performance Success in Corrosive Applications | CS-015
Project Profiles
Project Information
Client Name: | Confidential |
Location: | Milton, Saskatchewan, Canada |
Application: | Corrosion |
Initial Install Date: | August 2023 |
Product(s): | 1″ Grade D KeBond Coated Endless Rod |
Results Flyer: | Review the dollarized results here. |
Client challenge
Endless Rod (ER) manufactured using carbon and alloy steel is susceptible to corrosion and corrosion-initiated fatigue failures when used in rotary applications. As corrosion progresses, it leads to the formation pitting, which creates a stress riser, weakens the steel and increases the risk of mechanical failure due to progressive fatigue as shown in Figure 1.
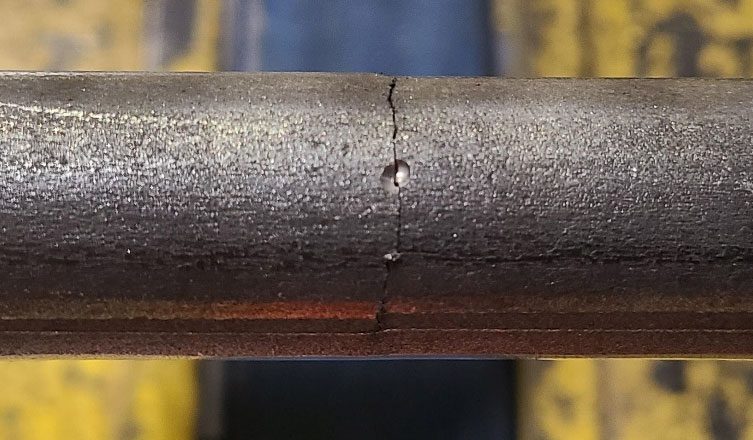
Ultimately, corrosion will accelerate costly repairs, maintenance, and downtime, underscoring the importance of proper material selection and protective measures in Progressing Cavity Pumping (PCP) applications.
Client Goals
In the Milton field located in Saskatchewan, Canada, our Client was faced with frequent rod failures due to corrosion. Several wells were selected as candidates for KeBond Coated Endless Rod, a durable, wear resistant, barrier coating that while intact will effectively prevent corrosion. Well1 included data from seventeen (17) workovers between June 2021 when the well was originally completed and August 2023 when KeBond was selected for installation. Well2 experienced four (4) workovers after original completion in February 2023 before KeBond was installed in August 2023. Many of these workovers were rod failures, with significant indication of corrosion on the workover reports. The base run time (BRT) established for technical success was 32 and 51 days respectively for each well. The target run time (TRT) was set at 180 days or 6 months for economic success based on the incremental cost of the coated KeBond product.
LS Solution
KeBond Coated Endless Rod is a 0.100in (2.54mm) thick, durable barrier coating that is both mechanically and chemically bonded to the bare steel rod using our proprietary coating process. With a lower coefficient of friction than bare steel, the applied coating is also very wear resistant in both Bare and Poly Lined Tubing when subjected to similar side loading conditions. After testing in Poly Lined Tubing, Figure 2 shows visual results for Bare ER while Figure 3 shows KeBond ER with an 80% reduction in wear under similar test conditions.
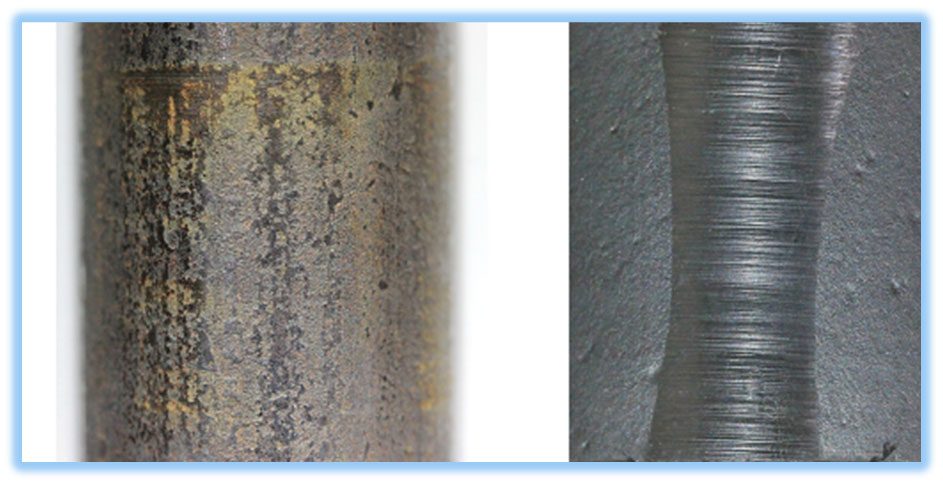
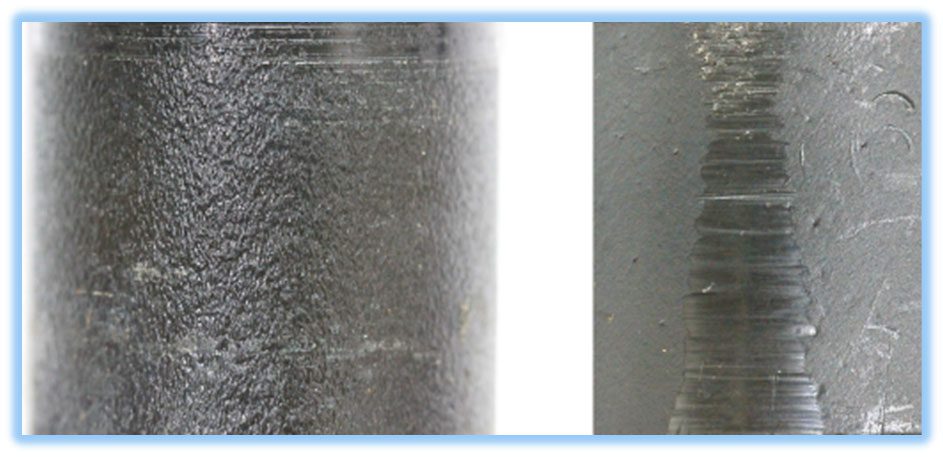
Sand and abrasives in the produced fluid tend to increase wear rates depending on the size, aggressiveness and concentration. Our internal wear testing program categorized the effects of wear with water and then with the addition of sand/abrasives in both bare and poly lined tubing. Figures 4 and 5 show the wear results of the stationary (tubing) and the rotary (rod) components as tested.
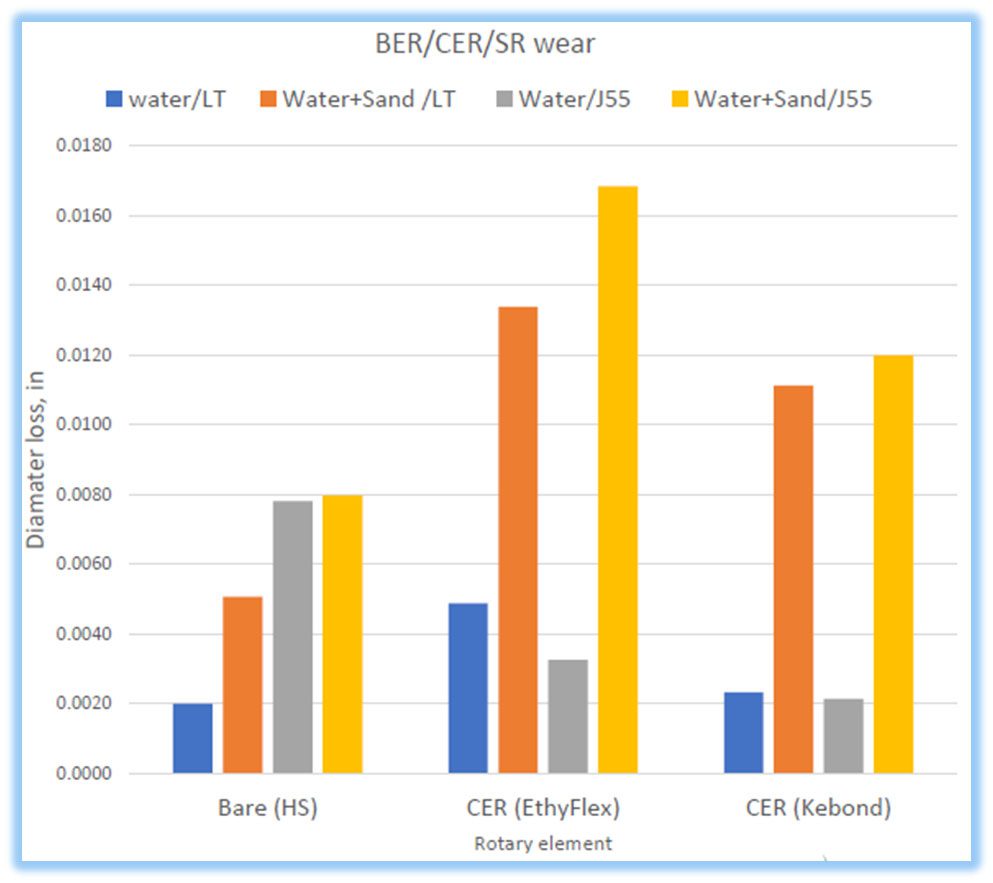
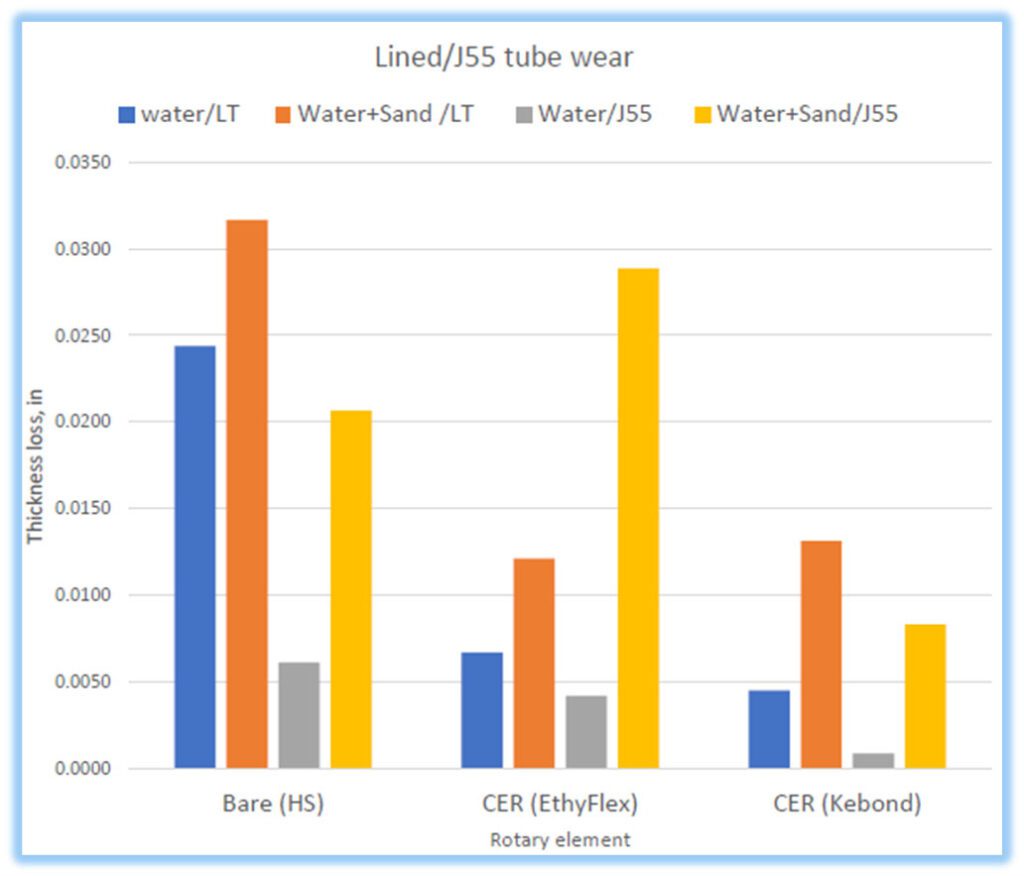
Operational Results
The deployment on the initial trial strings included D grade (1536 carbon steel) base rod coated with the KeBond. This is the lowest cost bare rod metallurgy, and lowest grade product for corrosion resistance. In the presence of a barrier coating, a corrosion resistant base is not required. Figure 6 shows the historical rod string performance of bare rod in Well1 compared to the KeBond installation which as of July 2024 has outperformed the established TRT for economic success by nearly 0.8x. This also represents a significant improvement over the BRT or technical success of 9.1x.
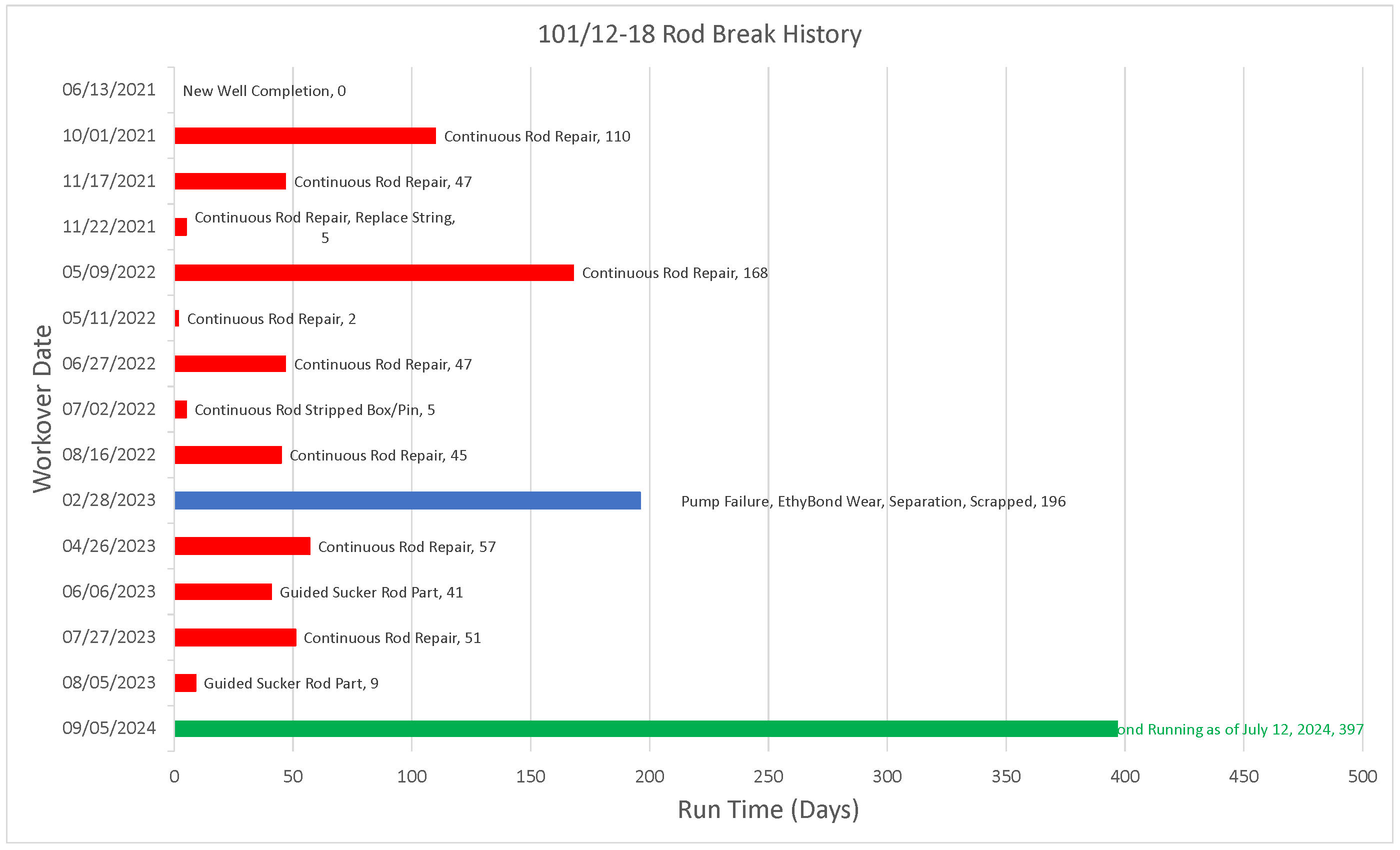
Well2 experienced similar results with Figure 7 showing a comparison of the second KeBond installation to the historical rod string performance of bare rod. This well was in the same area, and as you can see was plagued with poor overall rod performance mainly due to issues with corrosion-initiated fatigue. As of July 2024, the KeBond rod string has significantly outperformed previous strings with a 0.7x improvement on the TRT and 5.0x improvement over the BRT.
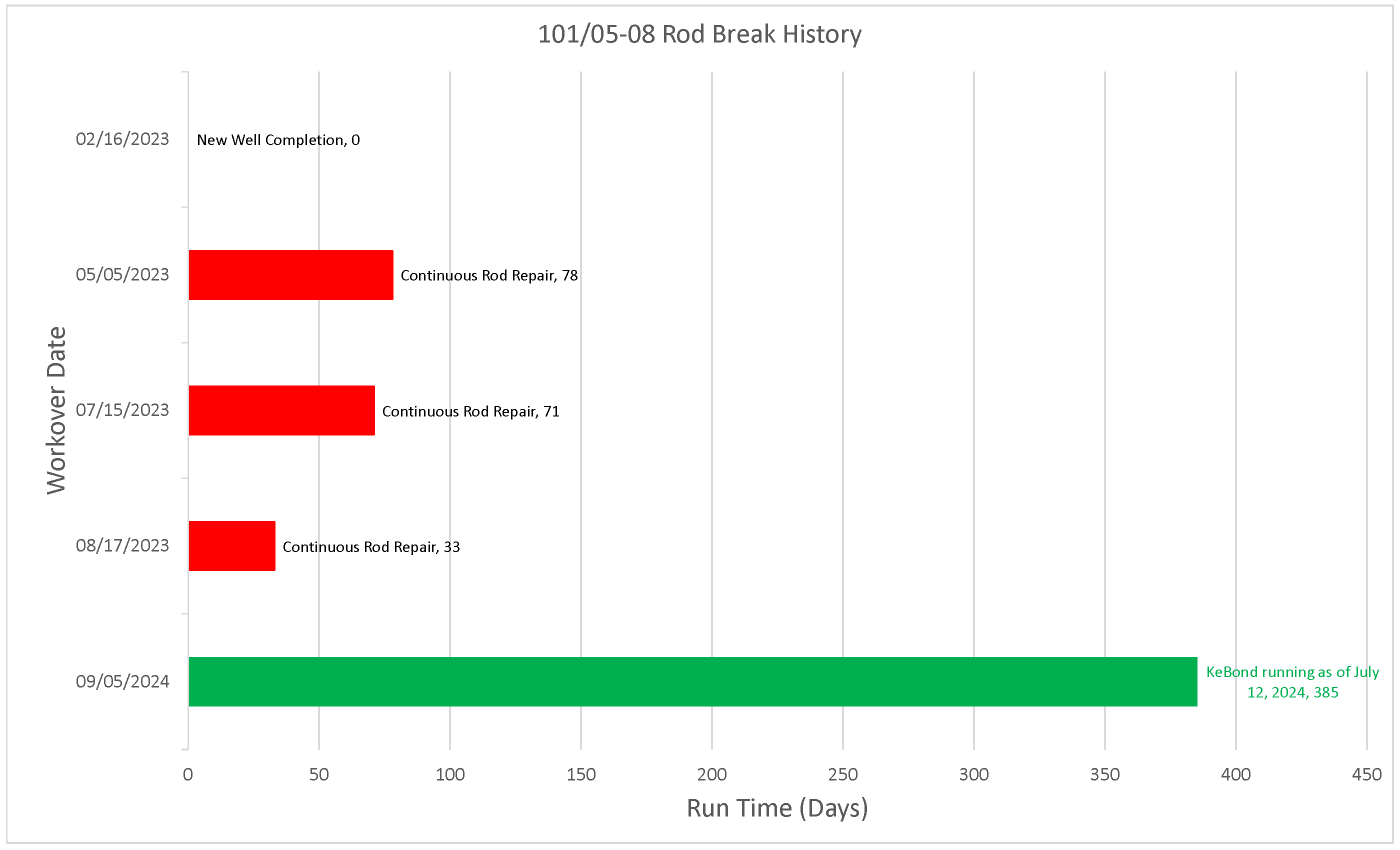
Conclusion
The KeBond has proven to be a very successful product in these applications with significant improvements in D grade rod string performance due to the elimination of corrosion and associated stress risers from pitting. The extent of these run life improvements becomes a function of the KeBond rod string wearability and the continued ability for the coating to provide long term corrosion resistance.
Let’s solve your lift challenges.
Reach out and Experience Performance with Lifting Solutions.