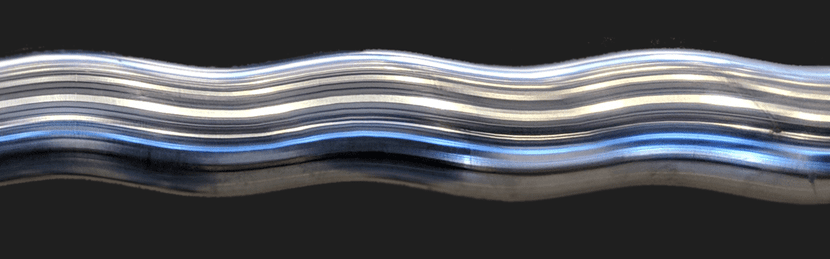
Runtime Increase with PivotAL PC Pump
Project Information
Client Name: | Confidential |
Location: | Bonnyville, Alberta, Canada |
Field Application: | Crude Bitumen |
Initial Install Date: | June 2021 |
LS Products and services: | PivotAL Progressing Cavity Pump |
Case summary
Oil production applications commonly experience a decline in production as the well matures, giving rise to challenges for existing equipment and the economic viability of the operation. This decline can be attributed to various factors, including stress-induced collapse and liquefaction in the region, gradual blockage of perforations by sand, lateral water coning, or the overall reduction in pressure due to the depletion of the solution-gas drive. These potential mechanisms of decline necessitate the implementation of unique workover strategies such as fluid loading, well cleanouts, reperforations, and sand hauling. However, these interventions significantly raise the operational costs associated with maintaining consistent inflow rates.
Frequent workovers that disrupt fluid inflow can have detrimental effects on the performance of downhole pumps. The alternating flows, characterized by the presence of sand or gas slugs, induce torque fluctuations in the downhole PC Pump and necessitate monitoring of the operating speed to adjust for changing inflow conditions. Consequently, these fluctuations and speed changes subject the rod string to varying stresses and loads. The heightened loads on the rod string escalate the risk of failure, leading to additional expenses for workovers that are already costly in their endeavors to maintain desired inflow rates. This financial burden quickly becomes unsustainable, ultimately compelling the decision to shut down or abandon the well.
To effectively address these challenges, Lifting Solutions has developed the PivotAL PC Pump as a specialized solution. This advanced pump incorporates an elongated stator coupled with a rotor comprising both active and inactive sections. In instances where the pump efficiency experiences a significant decline, a 12″ rod lift operation is executed, enabling the active sections of the rotor to be repositioned to previously unused sections of the stator. This strategic relocation of the rotor serves to restore and sustain the volumetric efficiency of the pump. By harnessing this innovative technology, the PC Pump can continue to operate effectively downhole, mitigating the risk of premature pump failures and minimizing the need for tubing workovers.
BACKGROUND – FREQUENT WORKOVERS
The specific well in question is categorized as a CHOPS (Cold Heavy Oil Production with Sand) well, characterized by a high fluid viscosity, elevated oil density, and a continuous influx of sand and abrasives. These unfavorable conditions presented significant production challenges that have been addressed through the implementation of frequent well loads and flushes. The purpose of these interventions is to enhance fluid inflow and remove accumulated sand deposits. However, these workovers not only escalate the operational expenses of the well but also have an adverse impact on the equipment and tools employed in lifting the fluid to surface.
The expedient of increasing the pump’s rotational speed, coupled with the augmented water influx, leads to an elevated number of rotations in the rod string, resulting in heightened wear rates on the tubing as well as alternating loads of the rod string. Wear is particularly pronounced in areas of high rod/tubing contact load (areas with high dog leg severity). Moreover, the presence of abrasives and sand in the produced fluid acts as cutting agents, exacerbating the degradation of both the elastomeric and metal surfaces. Slowing down the pump is not a viable solution to address the alternating loads on the rod string and tubing wear due to the low production rates caused by slippage. As a result, well loads are performed to maintain pump efficiency, necessitating higher operational speeds that generate significant fatigue scenarios, particularly in sections with the highest wellbore dogleg. Over time, these fatigue scenarios can lead to crack propagation and rod failure in areas experiencing high stress. The resulting breaks impose additional costs for fish and repair operations on the rod string.
Provided below are the Hours on Production of the well and the downhole pump, along with a chart of the conducted workovers. This is prior to the PivotAL PC Pump installation.
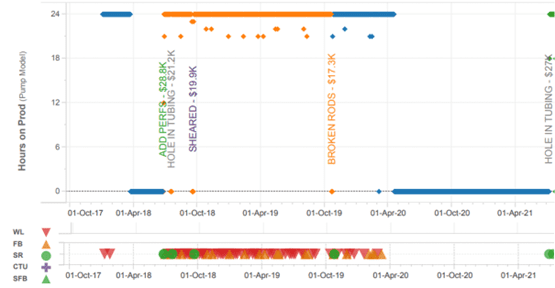
client challenge
Frequent well loads were implemented to enhance fluid inflow into the wellbore, which justified the economic viability of the well. However, these frequent fluctuations in flow rates resulted in detrimental effects on downhole equipment and tools. The increased rotational speed of the pumps led to erosions in the production tubing, causing downtime for the pump and necessitating expensive workovers. The escalation in operational speed elevated fatigue scenarios, exerting substantial stress on the rod string and ultimately resulting in rod failures. Operating conventional PC Pumps in this context was proving to be economically unsustainable due to the substantial operational costs associated with a relatively low-producing oil well combined with frequent workover operations involving the tubing and rod string.
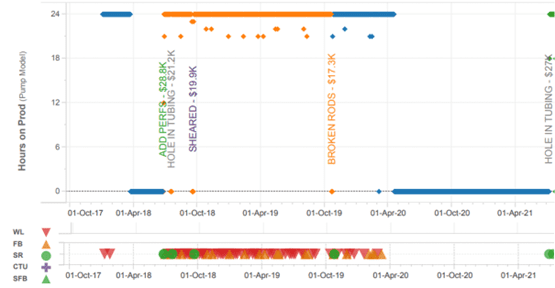
Pump Model | Reason for Workover | Run Days | Notes |
---|---|---|---|
5-1800 | Hole in Tubing | ~91 | Workover cost of $21,200 |
8-1800 | Broken Rods | 375 | Workover cost of $17,300 |
5-1800 | Hole in Tubing | 180 | Workover cost of $27,00 (well also shut in during the Covid-19 pandemic) |
8-1600-PivotAL | N/A | +690 | Position 1 ran 260 days, Position 2 running as of May 19, 2023 |
In response to these challenges, the client engaged Lifting Solutions to identify a suitable configuration capable of maintaining high pumping efficiency under varying downhole conditions while coping with the production of sand. Drawing on our extensive experience in similar applications involving conventional PC Pumps, Lifting Solutions leveraged a wealth of data to develop and implement a new technology. This technology was devised by their engineering and technical team to address the specific needs of the well and mitigate the adverse effects of alternating flow rates and sand production.
the ls solution
The application was equipped with Lifting Solutions’ PivotAL PC Pump to effectively address the operational challenges encountered by conventional PC Pumps. The PivotAL PC Pump incorporates an elongated stator and a custom-milled rotor featuring active and inactive sections spaced at 12-inch intervals. In cases where significant declines in pump efficiencies are observed, the rotor is elevated to the previously unutilized section of the stator. This relocation ensures the restoration of adequate pump efficiency while allowing the pump to remain deployed downhole.
This innovative technological advancement of the PivotAL PC Pump facilitates the preservation of optimal volumetric pump efficiencies. By maintaining high volumetric efficiencies, the pump can be operated at reduced speeds, leading to a decrease in the number of rotations of the rod string and consequent reduction in wear on both the rod and tubing. During the 12-inch lift operation, strategic repositioning of all couplings and areas with high tubing contact to different sections of the production tubing effectively minimizes wear spots and ensures the integrity of the tubing is preserved.
With the PivotAL PC Pump demonstrating the ability to maintain production efficiencies for an extended duration, the pump can be operated at slower speeds, mitigating the impact of alternating loads on the rod string, and significantly reducing the risk of premature rod failures and the need for fish and repair operations. Operating at slower speeds not only mitigates wear and fatigue but also sustains steady inflow rates, thereby reducing the frequency of well loads required to maintain consistent fluid inflow into the pump intake cavity.
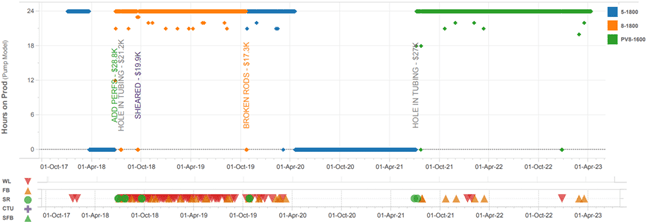
cONCLUSION
Through extensive consultations with our clients, the engineering and technical team at Lifting Solutions has developed an effective solution tailored to address challenging applications characterized by alternating fluid loads with sand. The PivotAL PC Pump has been specifically designed to maintain optimal volumetric efficiencies, enabling slower operational rates, and reducing tubing wear (via speed reduction and rod string repositioning), thereby mitigating the need for costly tubing workovers. This innovative solution is particularly suitable for wells with lower production rates that are prone to catastrophic elastomer damage, resulting in poor runtimes.
In the case of the specific well under consideration, the client had previously experienced pump and tubing workovers approximately every 214 days on average. However, following the installation of the PivotAL PC Pump (which remains operational as of May 19, 2023), a remarkable 223% improvement in runtime has been achieved compared to the historical average. This important extension in runtime significantly enhances the economic viability of the well, preventing the need to shut it down due to unfavorable economics.
Let’s solve your lift challenges.
Reach out and Experience Performance with Lifting Solutions.