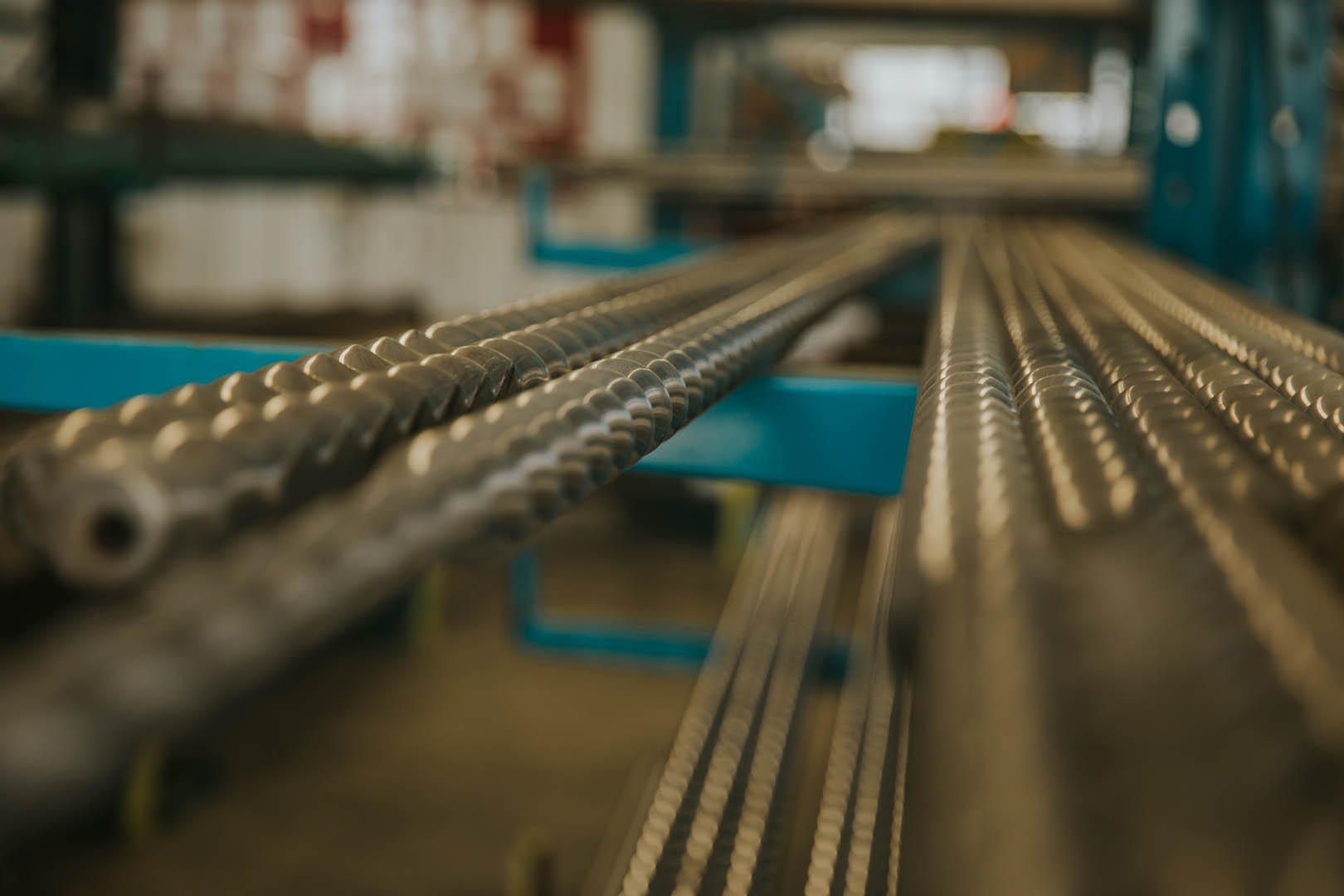
TorsionAL PCP Installation Success
Project Information
Location: | Lloydminster, Saskatchewan, Canada |
Application: | Heavy-Medium Crude Oil |
Product(s): | TorsionAL Progressing Cavity Pump |
Initial Install Date: | May 2019 |
Case summary
Progressing Cavity (PC) Pump rotors normally last many years, but when a rotor breaks prematurely it is normally due to fatigue. The eccentric movement of the rotor inside the stator can contribute to side loads, as well the tension from the rod string exerted on the rotor during operation can contribute to fatigue at the point where the rotor exits the stator. There are several engineering principles used to minimize fatigue in rotating equipment. Increasing the shaft diameter (in this case the rotor diameter), reducing the shaft length, ensuring concentric movement, using high quality materials, reducing stress concentrations and reducing operating loads.
The TorsionAL PC Pump from Lifting Solutions utilizes a large diameter, low eccentricity rotor, with shorter overall length. These geometric modifications resulted in several benefits including a stronger rotor with less nutation for each rotor rotation offset by a larger mass. The rotor is also safer/easier to pull free in situation where the rotor becomes sanded in and a flushby or coiled tubing workover is needed to free up the stuck pump. This unique geometry has a lower volume of elastomer which results in less diametral swell as a function of the rubber thickness.
BACKGROUND – REOCCURING BREAKS
After reviewing several wells with reoccurring rotor break problems, it was identified that as the wells were watering out, the produced rate, pumping speed and nominal pump volumes were increasing. This resulted in longer and longer pumps operating at higher speeds to achieve the desired production result. Several short pump run times required premature workovers due to broken rod and/or rotors. A design review was completed to look at the overall operating conditions, rod string loading conditions and the 7 year workover history. A snapshot of workovers related to rod/rotor breaks are detailed in Table 1 below.
Event | Pump Model | Reason for Workover | Run Days | Notes |
---|---|---|---|---|
New Pump | 27E1200 | Broken Rotor | 14 | Broken rotor, pump replaced with similar model |
New Pump | 27E1200 | Broken Rod | 65 | Rod repaired; pump upsized. |
New Pump | 47-1200 | Broken Rod | 80 | Broken rod, at bottom pin |
Same Pump | 47-1200 Retested | Broken Rod | 4 | Broken rod, 8in from the bottom pin |
Same Pump | 47-1200 Retested | Broken Rotor | 4 | Broken rotor, 24in from the rotor head |
New Pump | 45-1200 | Broken Rotor | 63 | Broken rotor, 12in from the rotor head |
Same Pump | 45-1200 | Broken Rod | 51 | Broken rod, no break location specified |
Same Pump | 45-1200 Retested | Broken Rod | 888 | Parted lower rod, unable to fish. Replaced rod string. |
New Pump | 45-1200 | Broken Rotor | 142 | Sucker rod above the rotor had broken pin end. |
CLIENT CHALLENGE
Rotor breaks require pulling of the tubing to repair resulting in expensive workover operations. At a minimum of $20,000 to surface the tubing and replace the pump, continued premature rotor breaks will result in a well becoming uneconomic. Once the well has been drilled, not much can be done about the wellbore trajectory and resulting dog leg severity. Changing conditions downhole over time result in shifting of the casing which can also lead to misalignment of the rotor and stator during operation downhole. With limited options available, our client looked to Lifting Solutions for options. Reverting to basic engineering principles for rotating shafts, we went to work on a fundamentally different pump geometry – a very ‘large’ idea that did not fit in with historical PCP design philosophy (low d/e, high eccentricity, weak rotors with optimized geometry focused on volume efficiency).
LS SOLUTION
The TorsionAL PC Pump was born with a rotor geometry that was very large and robust in diameter. It has a low eccentricity and smaller operational nutation. A rather inefficient design from the pump volume perspective that offered many advantages related to rotor strength and a potential to reduce side load with lower eccentricity and shorter overall lengths. The inefficient geometric design was offset by a larger overall diameter to maintain adequate capacity out of a shorter pump. Table 2 is a continuation of the previous table after introduction of the TorsionAL PC Pump and its advantages for combatting broken rotors.
Event | Pump Model | Reason for Workover | Run Days | Notes |
---|---|---|---|---|
New Pump | LS-TS 60-800 TorsionAL | Worn Pump | 1027 | Rod worn, replaced. Pump worn; L3 Inspection completed. |
New Pump | LS-TS 60-800 TorsionAL | RUNNING | 369 | Running as of March 2023 |
It is important to note that in addition to installation of the TorsionAL pump, we also recommended that a guided sucker rod was run one rod above the rotor to ensure that the continuous rod string in tension was not pulling back against the rotor while it was trying to complete its natural eccentric movement. More information on this recommendation can be found in our Technical Bulletin Library (LS-TB-031 Guided Rod above the Rotor).
CONCLUSION
By strategically evaluating workover history to better understand the problem at hand, Lifting Solutions along with our engineering and technical teams was able to provide meaningful recommendations to a reoccurring problem. This involved design of a low eccentricity, large diameter, short pump geometry that is focused on reducing rotor breaks in the right application. This unique design has strengths that can be leveraged at specific problems.
In this case the client went from rod/rotor breaks on average every 4-5 months to a runtime average of 2 years. This represents a four (4) times improvement over historical performance. This allowed them to keep this asset producing rather than adding it to the list of abandonment.
Let’s solve your lift challenges.
Reach out and Experience Performance with Lifting Solutions.